某食品公司生產鐵罐,日產量約10萬罐。過去長期使用控制圖控制罐頭的外觀缺陷。最近更新了生產線,生產穩定時罐頭外觀不良率小于0.01%。如果用控制圖進行控制,每個樣品至少要檢驗10000罐,檢驗量大,效率低,所以公司管理層決定放棄使用控制圖。但一段時間后,發現很多外觀有缺陷的易拉罐被退回,市場銷量明顯下降。
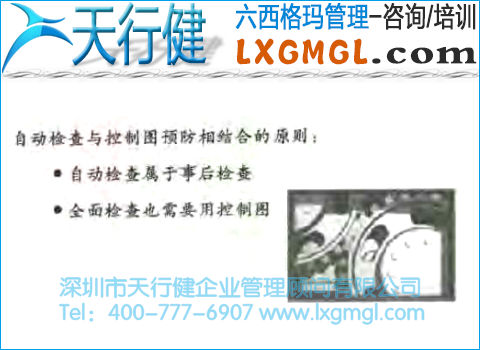
經過追溯發現,在生產穩定的時候,罐頭的外觀不良率確實低于0.01%,但是當生產線出現異常的時候,不良率會遠遠超過0.01%,有時甚至會在一個小時之內出現上百個不良產品,而這些不合格產品都會直接流入市場。
針對這種情況,公司決定引進自動檢測設備,可以快速自動檢測罐頭食品的外觀缺陷。此后,外觀有缺陷的罐頭食品不再進入市場,公司管理層認為這一問題已經解決。但很快就發現,雖然自動檢測保證了有缺陷的易拉罐不會再流入市場,但并不能保證生產線不會出現異常。有時幾天內會連續出現幾萬個外觀有缺陷的易拉罐,對這些有缺陷的易拉罐進行返工會造成很大的浪費。
于是公司決定重新使用控制圖來控制罐裝包裝過程。生產穩定時,每天生產的10萬罐中,有10多罐只會出現外觀缺陷。以每天生產的易拉罐為樣本,得出不合格率控制圖。重用控制圖后,不存在因外觀缺陷而大量返工的現象。
主站蜘蛛池模板:
黄色一级片免费网站
|
午夜影院
|
成人免费网站视频
|
亚洲中文日产2021
|
一级真人毛片
|
第一福利在线导航
|
avav片在线看
|
亚洲欧美日韩国产综合在线
|
国产乱码久久久久
|
在线?看视频91
|
久久精品国产精品亚洲综合
|
国产精品白丝久久av网站
|
yjizz视频|
未满小14洗澡无码视频网站
|
办公室特殊服务2在线观看
亚洲综合视频网站
|
高潮真紧好爽我视频
|
尤物AV无码国产在线观看
|
亚洲综合日韩精品欧美国产
|
国产青青青在线手机视频在线
|
亚洲天堂av网|
国产精品欧美三区
|
伊人蕉久中文字幕无码专区
|
午夜精品久久久久久久91蜜桃
|
日本黄色一级片视频
|
国产精品三区在线
|
中文字幕视频免费在线观看
|
中文字幕日日骚
|
全球AV集中精品导航福利
|
精品一区二区中文字幕
|
www视频在线免费观看
|
天天干天天天
|
美女总裁的贴身保镖短剧
|
人妻aⅴ无码一区二区三区
免费看黄网站免费网站
|
欧美日韩精品在线免费观看
|
欧美丰满熟妇bbbbbb百度
|
日韩三区三区一区区欧69国产
|
久久亚洲色WWW成人男男
|
邪恶久久|
天天爽视频
|
亚洲AV无码成人YELLOW
|
成人一级在线
|